Lots, and lots, and lots, of sanding today - not very interesting, but here's few progress pics.
Scraping the finish off the door panels after the stripper had some time to work.
I've filled up that little bucket of what I scrapped off everything else.

After all that sanding, I decided to stain everything prior to assembly.
There's still some trimming and details to cut, but little touch-ups are easier than flipping the cabs all around to stain after assembled.
Here's all the parts for one cab laid out.
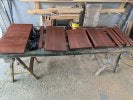
Stained and stacked to dry.
Touched up the head shell a bit to match how the rest turned out.
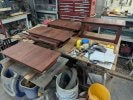
Hope to get some assembly done tomorrow.
After I get all the boxes together, I can get the baffles and back panels cut to fit.
Also need to cut the logo panel from one of those boards I milled down yesterday.
Scraping the finish off the door panels after the stripper had some time to work.
I've filled up that little bucket of what I scrapped off everything else.

After all that sanding, I decided to stain everything prior to assembly.
There's still some trimming and details to cut, but little touch-ups are easier than flipping the cabs all around to stain after assembled.
Here's all the parts for one cab laid out.
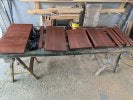
Stained and stacked to dry.
Touched up the head shell a bit to match how the rest turned out.
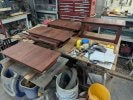
Hope to get some assembly done tomorrow.
After I get all the boxes together, I can get the baffles and back panels cut to fit.
Also need to cut the logo panel from one of those boards I milled down yesterday.