I've been working on this for a while.
Was figuring on a fairly high probability of complete "throw it in the burn pile" type of failure, so I didn't post any pics until I got it functional.
Started off with an ash slab I bought a year or so ago for another project that never materialized, traded a pedal for a custom made no-name tele neck, and found a cool piece of purpleheart wood at the local Rockler.
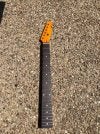
I got plenty of (100+) build pics to post, but I'm starting off with where I'm at with it now.
Still need to disassemble everything and get a final coat of clear (possibly multiple) on after the scuffs and such from assembly and testing.
So, here's the almost finished and functioning bookmatched purpleheart cap / ash back Cabronita Thinline.
The back of the body and neck are stained with "Phantom Gray", front of the headstock is stained black (awaiting a custom decal), and the purpleheart cap is nothing but clear lacquer.
Pups are GF'Trons Alnico V 6.6k / 6.0k set from Guitar Fetish, as is most of the hardware.
(Its' a clear pickguard with a black beveled edge, if you're wondering...)
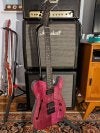

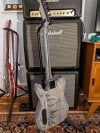
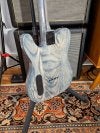
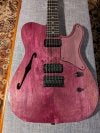
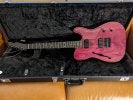
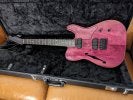
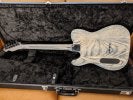
Special thanks to Russ (@Geeze ) for the technical consultations - he's seen some teaser pics in a PM.
Was figuring on a fairly high probability of complete "throw it in the burn pile" type of failure, so I didn't post any pics until I got it functional.
Started off with an ash slab I bought a year or so ago for another project that never materialized, traded a pedal for a custom made no-name tele neck, and found a cool piece of purpleheart wood at the local Rockler.
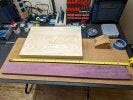
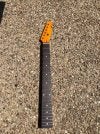
I got plenty of (100+) build pics to post, but I'm starting off with where I'm at with it now.
Still need to disassemble everything and get a final coat of clear (possibly multiple) on after the scuffs and such from assembly and testing.
So, here's the almost finished and functioning bookmatched purpleheart cap / ash back Cabronita Thinline.
The back of the body and neck are stained with "Phantom Gray", front of the headstock is stained black (awaiting a custom decal), and the purpleheart cap is nothing but clear lacquer.
Pups are GF'Trons Alnico V 6.6k / 6.0k set from Guitar Fetish, as is most of the hardware.
(Its' a clear pickguard with a black beveled edge, if you're wondering...)
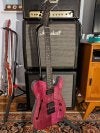

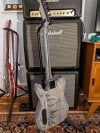
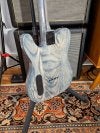
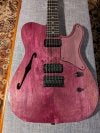
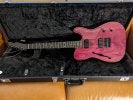
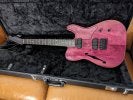
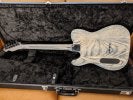
Special thanks to Russ (@Geeze ) for the technical consultations - he's seen some teaser pics in a PM.